How Plastic Extrusion in Utah is Helping Shape the Future of Manufacturing
- siliconeplastics
- May 28, 2024
- 4 min read
The Basics of Plastic Extrusion
Plastic extrusion is a manufacturing process where raw plastic material is melted and formed into a continuous profile. This method is commonly used to create products like pipes, tubing, and weatherstripping. Here are some key points about plastic extrusion:
Raw plastic material is fed into a hopper and then conveyed through a heated barrel
The material is melted and forced through a die, shaping it into a continuous profile
Various shapes and sizes can be achieved through different types of dies
Plastic extrusion offers high efficiency and versatility in creating a wide range of products
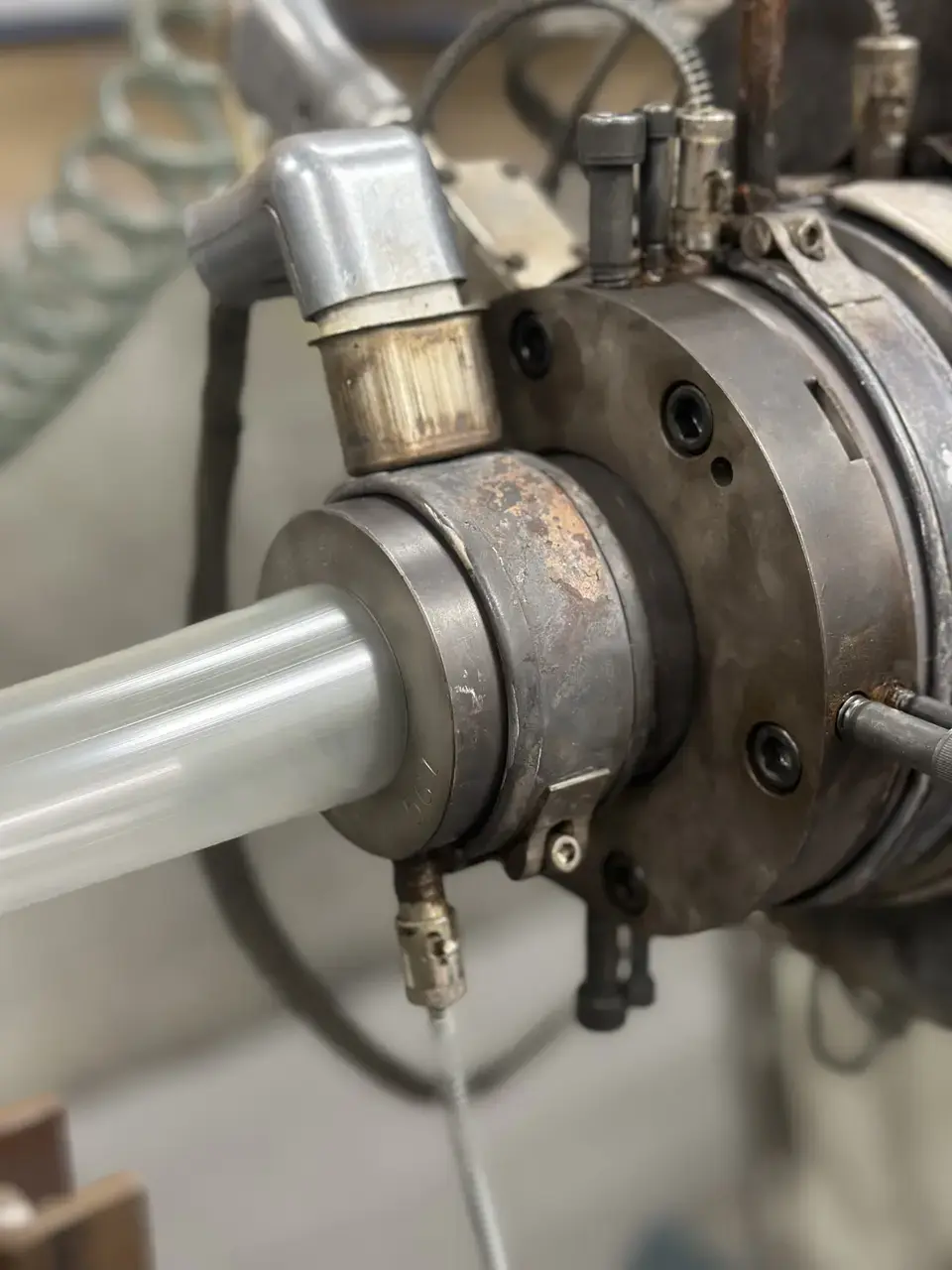
Importance of Plastic Extrusion in Manufacturing
Plastic extrusion in manufacturing is vital for creating products with consistent shapes and sizes. It allows for cost-effective production of various items like pipes, tubing, and profiles. The process of plastic extrusion in Utah is paving the way for innovative manufacturing techniques and helping industries meet their production demands efficiently.
Evolution of Plastic Extrusion Technology
Plastic extrusion technology has come a long way in shaping the manufacturing landscape. From simple beginnings, it has evolved into a versatile and efficient process. Today, advanced machinery and materials allow for precise control over the extrusion process, resulting in high-quality products. This evolution has led to increased productivity and cost-effectiveness in various industries, making plastic extrusion a vital component of modern manufacturing processes.
Key Benefits of Plastic Extrusion in Manufacturing
Plastic extrusion in manufacturing offers numerous benefits. Here are some key advantages you can expect from utilizing this process:
Cost-effective: Plastic extrusion can be a cost-effective manufacturing method, allowing for the production of complex shapes and designs at a lower cost.
Efficient production: The process of plastic extrusion is efficient, with high-speed production capabilities, leading to quicker turnaround times for your products.
Versatility: Plastic extrusion is versatile and can produce a wide range of products with varying shapes, sizes, and materials.
Consistent quality: With plastic extrusion, you can achieve consistent quality in your products, ensuring uniformity and reliability in your manufacturing process.
Plastic Extrusion Processes and Techniques
Plastic extrusion is a manufacturing process that creates shapes by melting raw plastic material and forcing it through a die. This process is commonly used to create various plastic products such as pipes, tubing, and profiles. Plastic extrusion in Utah employs different techniques like single screw extrusion and twin-screw extrusion to form the plastic into the desired shape. Single screw extrusion is a straightforward method, while twin-screw extrusion offers more precision and control over the final product. Additionally, blown film extrusion is a technique used to produce plastic films and sheets commonly found in packaging materials. Understanding these plastic extrusion processes and techniques can help in innovating and improving manufacturing practices for a sustainable future.
Role of Plastic Extrusion in Shaping the Future
Plastic extrusion plays a crucial role in shaping the future of manufacturing. It involves pushing raw plastic material through a die to create continuous shapes with a consistent cross-section. Here's why plastic extrusion is so important:
Cost-Effective: Plastic extrusion is a cost-effective way to produce plastic products in large quantities. It reduces the need for expensive molds and minimizes waste.
Versatile: This process can create a wide range of shapes and sizes, making it highly versatile for various industries such as automotive, construction, and packaging.
Customizable: Plastic extrusion allows for customization, enabling manufacturers to meet specific design requirements and produce unique products.
Efficient: It is an efficient and fast process, leading to increased productivity and reduced production time.
Overall, plastic extrusion in Utah is revolutionizing the manufacturing landscape by offering a sustainable, efficient, and flexible solution for producing high-quality plastic products.
Advancements in Plastic Extrusion in Utah
Plastic extrusion in Utah is at the forefront of manufacturing innovation. Companies in Utah are embracing advanced techniques to create high-quality plastic products efficiently. With the rise of technology, plastic extrusion has become more precise and cost-effective. Utah's expertise in this field is contributing to shaping the future of manufacturing, offering a glimpse into the endless possibilities of utilizing plastic extrusion in various industries.
Impact of Plastic Extrusion on Manufacturing Efficiency
Plastic extrusion plays a crucial role in improving manufacturing efficiency. It allows for the creation of complex shapes with high precision, reducing the need for additional machining processes. This results in faster production times and lower costs for manufacturers. Additionally, plastic extrusion enables the use of a wide range of materials, making it versatile for various industries, from automotive to packaging.
Sustainability and Environmental Impact of Plastic Extrusion
Plastic extrusion in Utah focuses on sustainability by using materials efficiently and minimizing waste. This process contributes to a lesser environmental impact compared to traditional manufacturing methods. Recycled materials are often incorporated in the production of extruded plastic products, reducing the demand for new raw materials. Additionally, the energy-efficient nature of plastic extrusion helps in minimizing the overall carbon footprint of manufacturing operations.
The Future of Manufacturing with Plastic Extrusion
Plastic extrusion in manufacturing offers numerous advantages, shaping the way products are made. In Utah and beyond, this technology is revolutionizing the industry by providing cost-effective solutions, flexibility in design, and efficient production processes. These benefits make plastic extrusion a key player in the future of manufacturing, driving innovation and enhancing product quality.
hokivip engine sold hokivip engine moon