Exploring the Benefits of Injection Production in Modern Industry
- siliconeplastics
- Oct 11, 2024
- 5 min read
Injection production has revolutionized modern manufacturing by offering efficient, cost-effective, and versatile solutions for creating a wide range of products. In this blog post, we will delve into the numerous benefits of injection production, exploring its impact on various industries and its significance in today’s economy.
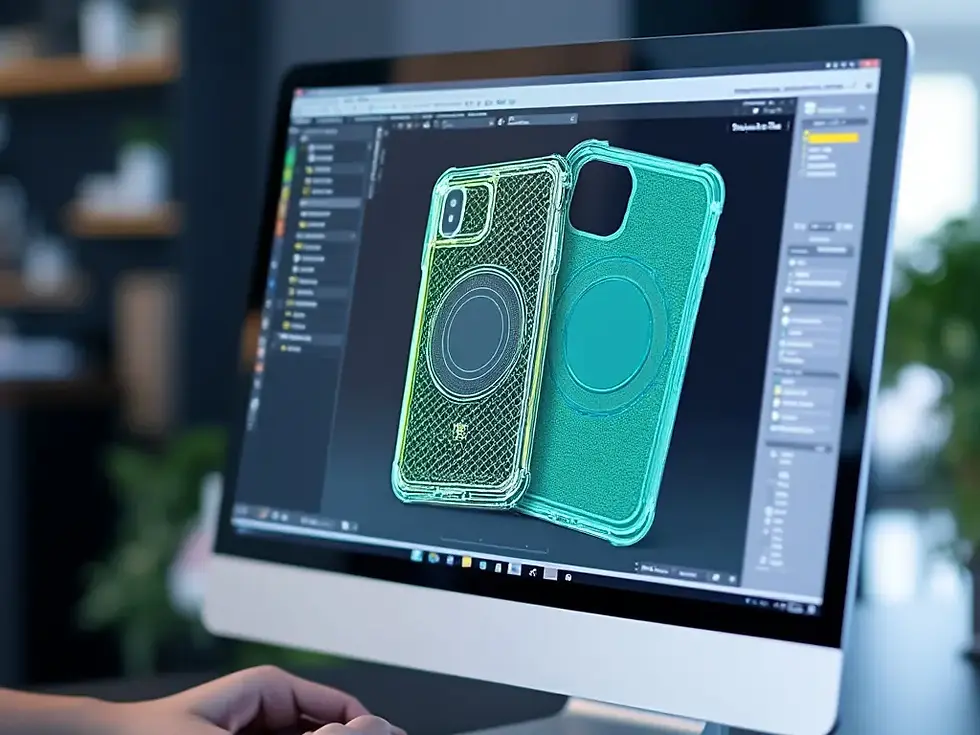
Understanding Injection Production
Injection production is a highly efficient manufacturing process that allows for the rapid production of complex shapes and high-volume goods. At its core, this method involves melting plastic or other materials and injecting them into a mold, which then solidifies to form the desired product. This fundamental understanding of injection production sets the stage for appreciating its broad applications across various industries.
This technique has become particularly popular in sectors such as automotive, consumer goods, and medical devices. The versatility and adaptability of injection production enable manufacturers to respond swiftly to market demands while minimizing waste and optimizing resources. By producing items in large quantities, businesses can enjoy cost savings that translate into lower prices for consumers.
Moreover, the technology behind injection production has advanced significantly over the years. With the integration of computerized systems and sophisticated machinery, manufacturers can achieve higher precision and faster turnaround times than ever before. Understanding these technological advancements enhances our grasp of why injection production continues to thrive in modern manufacturing.
The Key Advantages of Injection Production
One of the primary advantages of injection production is its ability to produce highly consistent and uniform parts. This is particularly crucial in industries where precision is paramount, such as aerospace and electronics. When each part meets exact specifications, companies can ensure the reliability and safety of their products. Thus, consistency not only improves quality but also strengthens brand trust.
In addition to consistency, injection production offers remarkable efficiency. The speed of the injection molding process means that large volumes of products can be manufactured in a short time, greatly enhancing productivity. This efficiency becomes especially beneficial during peak production periods, allowing businesses to scale operations quickly without compromising on quality or performance.
Furthermore, injection production can significantly reduce labor costs. Automation in the molding process minimizes the need for manual intervention, leading to a workforce that can focus on value-added tasks rather than repetitive operations. As a result, businesses can improve their operational efficiency while reallocating their workforce to areas that enhance innovation and development.
Cost Efficiency and Productivity Boost
When it comes to manufacturing, cost efficiency is often a top priority. Injection production shines in this area, as it reduces the material waste typically associated with traditional manufacturing processes. The accurate material usage in this method leads to significant savings, making it an attractive option for businesses looking to maintain competitiveness in a fast-paced marketplace.
Moreover, the initial investment in injection production equipment may seem substantial, but the long-term savings far outweigh these costs. The capability to produce large quantities of a product with minimal waste results in better overall cost management. By analyzing the return on investment over time, many companies discover that injection production quickly pays for itself through increased productivity and decreased material costs.
Investing in injection production not only boosts productivity but also creates room for innovation. The time saved in the production cycle can be allocated to research and development, enabling companies to explore new designs, materials, and technologies. This cycle of continuous improvement is vital for businesses aiming to stay ahead in their respective fields.
Ultimately, the productivity benefits generated through injection production contribute to a company's ability to meet global demand quickly and efficiently. With rapid product turnover and the capacity for customization, businesses can adapt to changing market needs, resulting in increased market share and customer satisfaction.
Versatility in Material Usage
Another remarkable advantage of injection production is its versatility in material usage. This process is not limited to just plastics; it can also accommodate a wide range of materials, including metals, fabrics, and composites. This flexibility allows manufacturers to select the best material suited for their specific product requirements, enhancing functionality and performance.
For example, in the automotive industry, manufacturers can use specialized thermoplastics that are lightweight yet durable, improving fuel efficiency while maintaining safety standards. Similarly, in the consumer electronics sector, injection production can create sleek and lightweight casings that appeal to modern aesthetics while providing protection to sensitive components.
In addition to accommodating different materials, injection production allows for the integration of multiple features into a single part. This capability simplifies the manufacturing process and reduces assembly time, translating to further cost savings and efficiency gains. The option to create components that include multiple functionalities demonstrates just how versatile injection production can be.
Enhancing Product Design and Complexity
The design freedom offered by injection production is unparalleled. Designers can trial intricate shapes and features that would be impossible or prohibitively expensive to produce with traditional methods. This ability to craft sophisticated designs not only yields aesthetically pleasing products but also allows for innovative functionality that meets modern consumer expectations.
Complex geometries, undercuts, and detailed engravings can be easily incorporated into the mold design, enabling manufacturers to create products that stand out in a crowded marketplace. This means businesses can maintain a competitive edge by responding to trends and consumer demands with unique offers.
Moreover, the rapid prototyping capabilities of injection production allow companies to test and iterate on designs swiftly. By creating prototypes quickly, product development cycles can be shortened, giving businesses the agility to capture market opportunities or pivot in response to customer feedback. This aligns perfectly with the principles of lean manufacturing, which aim for efficiency and responsiveness.
Sustainability and Environmental Benefits
Sustainability has become a crucial consideration in manufacturing today, and injection production plays a significant role in reducing environmental footprints. The precision of this method leads to minimal waste generation, as materials are used efficiently throughout the production process. As companies strive to improve their eco-friendly credentials, injection production provides a path towards more sustainable practices.
Furthermore, many materials used in injection production are recyclable, adding to its sustainability credentials. By choosing sustainable materials and implementing recycling protocols, businesses can significantly reduce their overall impact on the planet. This not only aligns with regulatory standards but also appeals to environmentally conscious consumers who prioritize sustainability when making purchasing decisions.
Additionally, advancements in bio-based plastics and other eco-friendly materials present new opportunities for injection production. Companies can now explore innovative formulations that are both functional and less harmful to the environment, enhancing the attractiveness of their products while promoting sustainable practices in their operations.
Case Studies: Successful Applications of Injection Production
Real-world applications of injection production highlight its transformative impact across different industries. For instance, in the automotive sector, manufacturers have leveraged injection production to create complex parts with precision and speed. This has enabled them to develop lighter vehicles that comply with regulatory standards for emissions while remaining cost-effective.
Moreover, the consumer goods industry has benefited immensely from injection production. By producing a variety of packaging solutions using this method, companies have been able to introduce innovative designs that enhance user experience while reducing waste. These applications exemplify the journey from concept to market, showcasing how injection production facilitates creativity and practical solutions.
In the healthcare sector, injection production has played a pivotal role in the advancement of medical devices. The ability to manufacture precise and sterile components has revolutionized how medical equipment is developed and produced. This has not only improved patient outcomes but has also streamlined the production processes, ultimately saving time and resources.
Wrapping Up the Impact of Injection Production
In summary, injection production stands as a cornerstone of modern manufacturing, providing unparalleled advantages in efficiency, quality, and sustainability. Its ability to adapt to different materials and produce complex shapes highlights its importance in meeting the diverse needs of various industries. As technology continues to evolve, the future of injection production looks promising, paving the way for innovative solutions and advancements in manufacturing.
https://www.chalkandcheese.in
https://learnicocollege1.mkcl.org
https://byggoutletnorge.no/