How Does Plastic Extrusion Work in Utah?
- siliconeplastics
- Feb 28
- 4 min read
Plastic extrusion is a widely used manufacturing process in Utah, playing a critical role in producing a variety of plastic products. This blog explores the fundamentals of plastic extrusion, its applications in Utah, and the advantages it offers to manufacturers and consumers alike.
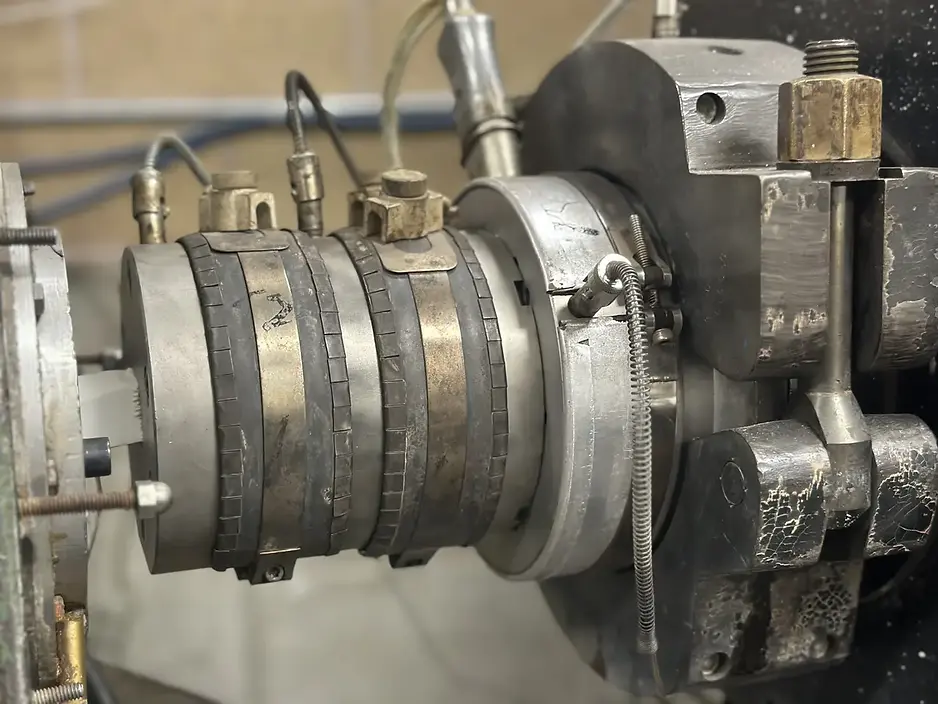
Understanding the Basics of Plastic Extrusion
Plastic extrusion involves melting plastic and forcing it through a mold called a sizer to create a continuous shape. This section will delve into the mechanical processes and technologies that underpin this manufacturing technique.
To understand plastic extrusion, one must consider the equipment used in this process. The extruder is the heart of the operation, with its barrel and screw working in harmony to transport the plastic pellets, melt them down, and force the molten plastic through the die. This intricate machinery is essential in controlling heat and pressure, ensuring quality results.
Moreover, the versatility of this process is remarkable. Plastic extrusion isn't limited to one form or function; instead, it can create a myriad of profiles, including sheets, tubes, and complex custom shapes. This flexibility makes it a preferred choice for manufacturers looking to innovate and tailor solutions to specific market needs in Utah.
Materials Used in Plastic Extrusion
Various types of plastics can be used in extrusion, ranging from polyethylene to polystyrene. This section will discuss the characteristics of these materials and why they are suitable for the extrusion process.
Polyethylene, known for its durability and flexibility, is one of the most common choices in plastic extrusion. Its low density allows for easy processing, making it ideal for everything from grocery bags to packaging material. In contrast, polystyrene, while less flexible, offers rigidity and is widely utilized in creating insulative products and components in electronic devices.
Additionally, more advanced materials like polypropylene and PVC are also prominent in Utah's plastic extrusion scene. Polypropylene exhibits excellent impact resistance and thermal stability, while PVC’s resilience and variety of formulations open doors to various applications, from construction materials to medical devices.
The Plastic Extrusion Process Explained
From the feeding of raw materials to cooling the extruded product, this section will outline the step-by-step process involved in plastic extrusion and highlight the importance of each stage.
Initially, plastic pellets are fed into the hopper of the extruder. As they descend, they are gradually heated by the barrel's heaters, which melt the plastic. This melting process is critical; any miscalculation in temperature could result in inconsistent product quality. Once melted, the plastic is transported forward by the screw, where it's subjected to shear forces that completely liquefy it.
Next, the molten plastic is forced through the die, which shapes it into the desired form. The configuration of the die is vital, as it directly influences the final product's dimensions and properties. Following extrusion, the material is typically cooled—often with a water bath or air-cooling system—to solidify before being cut or rolled into usable forms.
Applications of Plastic Extrusion in Utah
Utah's industries benefit significantly from plastic extrusion, from packaging to automotive parts. This section will explore various applications and real-world examples of how Utah-based companies utilize this process.
In the packaging sector, companies in Utah leverage plastic extrusion to manufacture containers, trays, and films that are lightweight yet durable. The flexibility of this method allows for the creation of tailored packaging solutions designed to meet the specific needs of both consumer products and industrial applications.
Additionally, the automotive industry in Utah has embraced plastic extrusion for producing components such as bumpers, interior trim pieces, and thermal insulation. The ability to create intricate shapes while maintaining structural integrity makes plastic extrusion an invaluable asset for manufacturers aiming to enhance vehicle efficiency and aesthetics.
Advantages of Plastic Extrusion for Manufacturers
Plastic extrusion offers numerous benefits, including cost-effectiveness, efficiency, and the ability to produce complex shapes. This section will examine these advantages and their implications for manufacturers in Utah.
One of the most significant advantages is the capacity for high-volume production. Once the die is created, the extruder can operate continuously, churning out large quantities of products without the need for frequent setup changes. This leads to reduced labor costs and increases overall productivity, helping manufacturers in Utah remain competitive.
Moreover, plastic extrusion minimizes waste compared to other manufacturing methods. Excess materials can be recycled and fed back into the system, enhancing sustainability efforts. This not only saves costs but also aligns with the growing consumer demand for environmentally conscious products, making it a smart choice for businesses in Utah looking to improve their ecological footprint.
Challenges and Considerations in Plastic Extrusion
Like any manufacturing process, plastic extrusion comes with its challenges, such as material wastage and machine maintenance. This section will address these issues and discuss strategies to mitigate them.
One challenge that manufacturers face is ensuring the quality of the extruded products. This often requires rigorous quality control measures to inspect dimensions and detect any inconsistencies. Implementing real-time monitoring systems can aid in identifying problems early, allowing for quick adjustments to minimize defects.
Furthermore, the maintenance of extrusion machinery is paramount. Regular servicing and timely replacement of worn-out parts can prevent costly downtimes. Manufacturers in Utah benefit from establishing scheduled maintenance routines, which not only prolong machinery lifespan but also ensure optimal performance during production runs.
Wrapping Up: The Impact of Plastic Extrusion in Utah
In conclusion, understanding how plastic extrusion works provides valuable insights into its significance in Utah's manufacturing landscape. With its efficiency and versatility, plastic extrusion continues to shape the industry and meet the demands of various sectors.
Comments