The Essential Guide to Understanding Injection Mold Design for Entrepreneurs
- siliconeplastics
- Jul 11, 2024
- 3 min read
Diving into the world of injection mold design can be both daunting and exciting for entrepreneurs seeking to bring their innovative ideas to life. Understanding the intricacies of this process is crucial for ensuring the production of high-quality products efficiently and cost-effectively. In this guide, we will explore the fundamental principles, optimization strategies, design considerations, and innovative approaches that will empower entrepreneurs to make informed decisions when it comes to injection mold design.
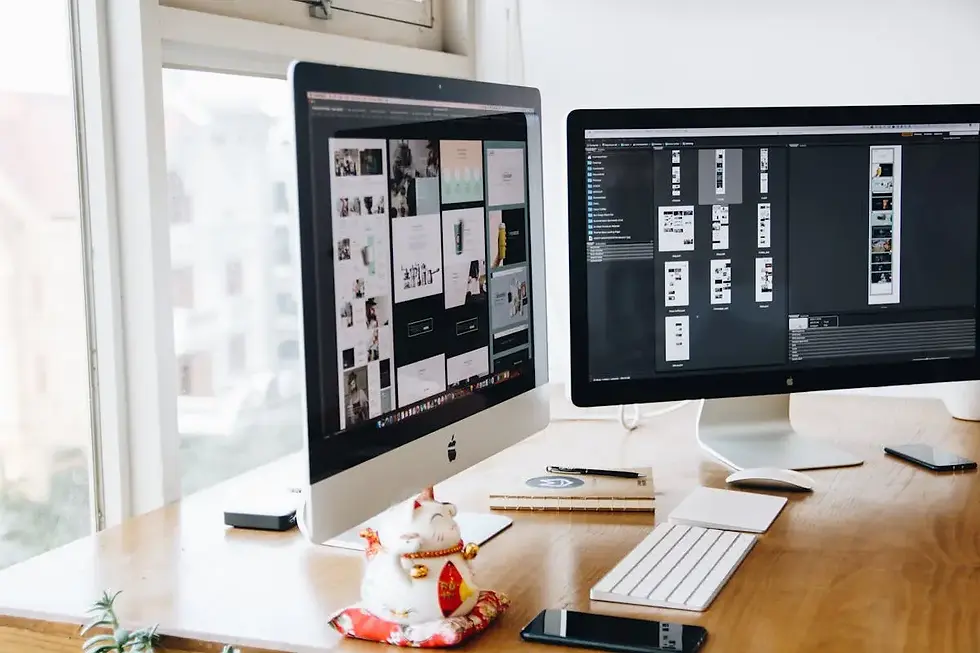
The Fundamentals of Injection Mold Design
Understanding the fundamentals of injection mold design is the cornerstone of developing a successful manufacturing process. From selecting the right materials to meticulously designing the mold cavity, every decision made at this stage has a direct impact on the quality and efficiency of the final product. Entrepreneurs embarking on this journey must grasp the importance of factors such as cooling time, gate location, and parting lines to optimize the injection molding process.
Incorporating principles of mold design such as draft angles, wall thickness uniformity, and venting solutions are essential in preventing defects like warping, sink marks, and air traps in the molded parts. By paying attention to these minute details, entrepreneurs can ensure that their products meet quality standards and are visually appealing to consumers.
Moreover, a thorough understanding of the different types of molds, including prototype molds, production molds, and multi-cavity molds, allows entrepreneurs to tailor their design approach based on the scale and complexity of their production needs. By mastering the fundamentals of injection mold design, entrepreneurs can lay a solid foundation for their manufacturing endeavors.
Optimizing the Injection Molding Process
Optimization is key to enhancing the injection molding process for maximum efficiency and productivity. Entrepreneurs can achieve this by fine-tuning parameters such as injection speed, pressure, and temperature to minimize cycle times and reduce material wastage.
Utilizing advanced techniques like scientific molding and computer-aided engineering software empowers entrepreneurs to simulate and analyze the molding process before production, enabling them to identify potential issues and make preemptive adjustments. By embracing data-driven decision-making, entrepreneurs can streamline their operations and deliver consistent, high-quality products.
Continuous improvement is at the core of optimizing the injection molding process. By leveraging real-time monitoring systems, entrepreneurs can gather valuable insights into the performance of their molds, enabling them to make data-driven decisions that drive efficiency and quality in their manufacturing processes.
Design Considerations for Cost-Effective Production
Balancing cost-effectiveness and quality in injection mold design requires strategic decision-making and a keen eye for detail. Entrepreneurs must evaluate factors such as tooling expenses, material selection, and production volume to optimize their manufacturing costs while maintaining product integrity.
Designing for manufacturability is essential in minimizing production costs and reducing lead times. By collaborating closely with mold designers and manufacturers, entrepreneurs can streamline the design process, identify potential cost-saving opportunities, and achieve a balance between design complexity and manufacturing feasibility.
Furthermore, exploring innovative solutions such as additive manufacturing for rapid prototyping and tooling can significantly accelerate the product development cycle and reduce upfront costs for entrepreneurs. By embracing cost-effective design considerations, entrepreneurs can enhance their competitive edge in the market while delivering value to their customers.
Innovative Approaches in Injection Mold Design
Innovation is the driving force behind transformative injection mold design practices that revolutionize the way products are manufactured. Entrepreneurs who adopt cutting-edge technologies like 3D printing for mold fabrication or implement eco-friendly materials in their injection molding processes can differentiate themselves in the market and appeal to environmentally conscious consumers.
Collaborating with materials scientists and engineers to explore novel resin formulations and sustainable alternatives paves the way for entrepreneurs to create innovative and environmentally friendly products. By staying ahead of industry trends and embracing novel approaches in injection mold design, entrepreneurs can position themselves as industry leaders and drive positive change in the manufacturing sector.
Embracing a culture of experimentation and continuous learning is essential for entrepreneurs looking to push the boundaries of traditional injection mold design. By fostering a creative and collaborative environment within their teams, entrepreneurs can inspire innovation and drive forward-thinking solutions that resonate with today's dynamic market demands.
In conclusion, the realm of injection mold design offers a wealth of opportunities for entrepreneurs to innovate, create, and disrupt traditional manufacturing processes. By mastering the fundamentals, optimizing their operations, considering cost-effective design solutions, and embracing innovation, entrepreneurs can navigate the complexities of injection mold design with confidence and drive sustainable growth in their ventures.
Empowering Entrepreneurs Through Innovation
As an entrepreneur navigating the realm of injection mold design, it is vital to remember that innovation and creativity play pivotal roles in shaping the success of your manufacturing processes. By staying informed about the latest trends, leveraging cost-effective design strategies, and embracing innovation, you can stay ahead of the curve in the competitive landscape of product development. Let your passion for injection mold design drive you towards creating impactful and efficient solutions that resonate with your target market.
Comentarios