The Future of Manufacturing: Innovations in Plastic Extrusion Technology
- siliconeplastics
- Jul 4, 2024
- 4 min read
In a world rapidly advancing in technological innovations, the future of manufacturing stands at the forefront of progress. The intricate realm of plastic extrusion technology is no exception, with continuous advancements shaping the way we produce everyday items. Join us on a journey through the latest trends and breakthroughs revolutionizing the plastic extrusion landscape.
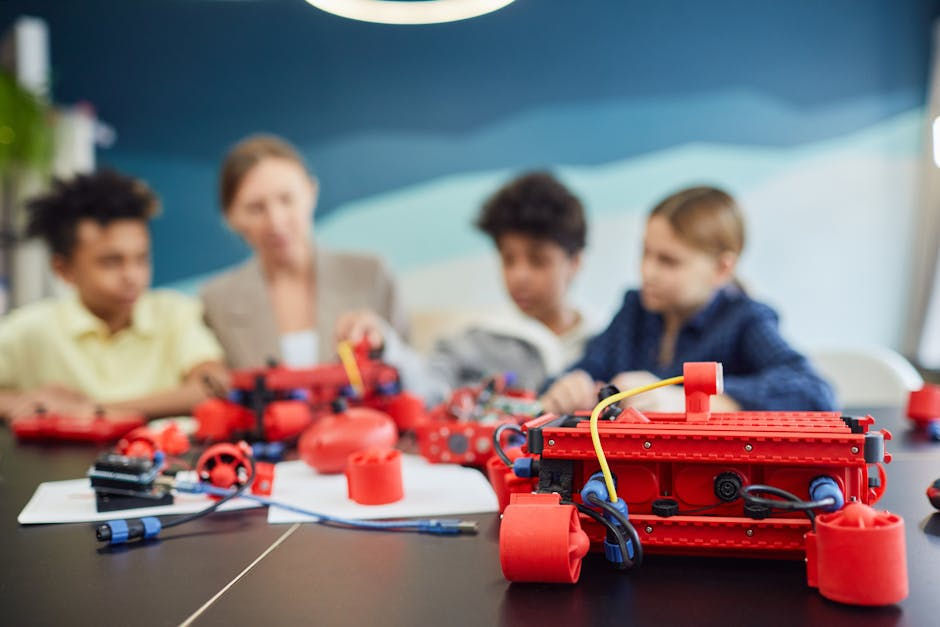
Advancements shaping the plastic extrusion landscape
In the realm of plastic extrusion, innovation is the beating heart driving progress forward. From the development of high-speed extrusion machinery to the integration of IoT technology for real-time monitoring, the landscape is evolving at a remarkable pace. These advancements not only enhance production efficiency but also open doors to novel applications across various industries.
One of the key trends influencing plastic extrusion is the move towards sustainable practices. Manufacturers today are increasingly embracing biodegradable polymers and recycled materials in their extrusion processes. This shift towards eco-friendly alternatives underscores a collective commitment towards reducing environmental impact without compromising on quality or performance.
Moreover, precision in extrusion has reached unprecedented levels, thanks to cutting-edge technologies such as laser gauging systems and automated control systems. These innovations ensure consistent material thickness and dimensional accuracy, revolutionizing the quality standards in plastic extrusion. The result is a seamless production process that delivers products with uncompromised precision.
The integration of artificial intelligence (AI) and machine learning algorithms is another game-changer in plastic extrusion technology. By analyzing vast amounts of data in real time, AI algorithms optimize extrusion parameters, predict maintenance needs, and detect potential defects, thereby enhancing overall operational efficiency and product quality.
Furthermore, advancements in material science have led to the development of specialized polymers tailored for specific extrusion applications. Whether it's enhancing thermal stability, improving mechanical properties, or achieving desired surface finishes, these advanced polymers are expanding the horizons of what is achievable through plastic extrusion.
Revolutionizing production with cutting-edge extrusion techniques
The future of manufacturing lies in the transformative power of cutting-edge extrusion techniques. Ultrasonic welding, 3D printing, and co-extrusion are among the innovative methods reshaping the production landscape. These techniques not only offer enhanced productivity and cost efficiency but also unlock new possibilities in product design and customization.
Ultrasonic welding, for instance, enables the seamless joining of thermoplastic components without the need for adhesives or additional materials. This technique not only accelerates production cycles but also ensures strong and durable bonds, making it ideal for applications requiring precision and reliability.
Similarly, 3D printing in plastic extrusion has revolutionized rapid prototyping and customized production. By layering molten thermoplastic materials based on digital designs, manufacturers can create complex geometries and intricate parts with unparalleled precision. This additive manufacturing process is driving innovation across industries, from aerospace to healthcare.
Co-extrusion, on the other hand, allows for the simultaneous extrusion of multiple materials to create composite products with unique properties. By combining different polymers or additives during the extrusion process, manufacturers can achieve functionalities such as barrier resistance, color variations, or enhanced strength in a single operation, streamlining production and diversifying product offerings.
Moreover, the integration of Industry 4.0 principles into extrusion processes is revolutionizing production efficiency and flexibility. Smart factories equipped with interconnected systems, robotics, and real-time analytics are optimizing production workflows, reducing downtime, and enabling predictive maintenance in the plastic extrusion industry.
Sustainability at the core of future extrusion innovations
The future of plastic extrusion technology is intrinsically linked to sustainability, with a growing emphasis on eco-friendly practices and materials. Recycling initiatives, renewable energy sources, and closed-loop systems are becoming integral components of extrusion processes, reflecting a commitment to environmental stewardship and resource conservation.
One of the innovative approaches towards sustainable extrusion is the incorporation of post-consumer recycled materials into the production cycle. By reusing plastics derived from consumer waste, manufacturers can reduce dependency on virgin resins, minimize landfill waste, and contribute to a circular economy model that promotes resource efficiency and waste reduction.
Furthermore, advancements in energy-efficient extrusion technologies, such as heat recovery systems and intelligent heating controls, are lowering the environmental footprint of manufacturing operations. By optimizing energy consumption and reducing greenhouse gas emissions, these technologies are paving the way for a more sustainable future for the plastic extrusion industry.
In addition, bio-based polymers derived from renewable sources like corn starch, sugarcane, or algae are revolutionizing material choices in plastic extrusion. These biodegradable and compostable polymers offer a greener alternative to traditional plastics, addressing concerns related to plastic pollution and contributing to the shift towards a more sustainable and circular economy.
The integration of sustainable practices not only benefits the environment but also enhances brand reputation and consumer perception. Forward-thinking manufacturers embracing sustainable extrusion innovations are not only aligning with global sustainability goals but also paving the way for a more resilient and environmentally conscious manufacturing sector.
Pioneering the Future
As we gaze into the future of manufacturing, it is undeniable that plastic extrusion technology will play a pivotal role in shaping industries across the globe. The relentless pursuit of efficiency, sustainability, and precision in extrusion processes promises a future where innovation knows no bounds. With each advancement, we move closer to a world where possibilities in manufacturing are as endless as the polymers used in plastic extrusion.
Comments