The Ultimate Guide to Choosing the Right Plastic for Your Project
- siliconeplastics
- Aug 1, 2024
- 4 min read
Embarking on a project involves a crucial decision-making process, especially when it comes to selecting the perfect plastic. Understanding the intricacies of various plastic materials, manufacturing techniques, and cost considerations can significantly impact the success of your project. Join us on a comprehensive journey to explore the essential aspects of choosing the right plastic for your next endeavor.
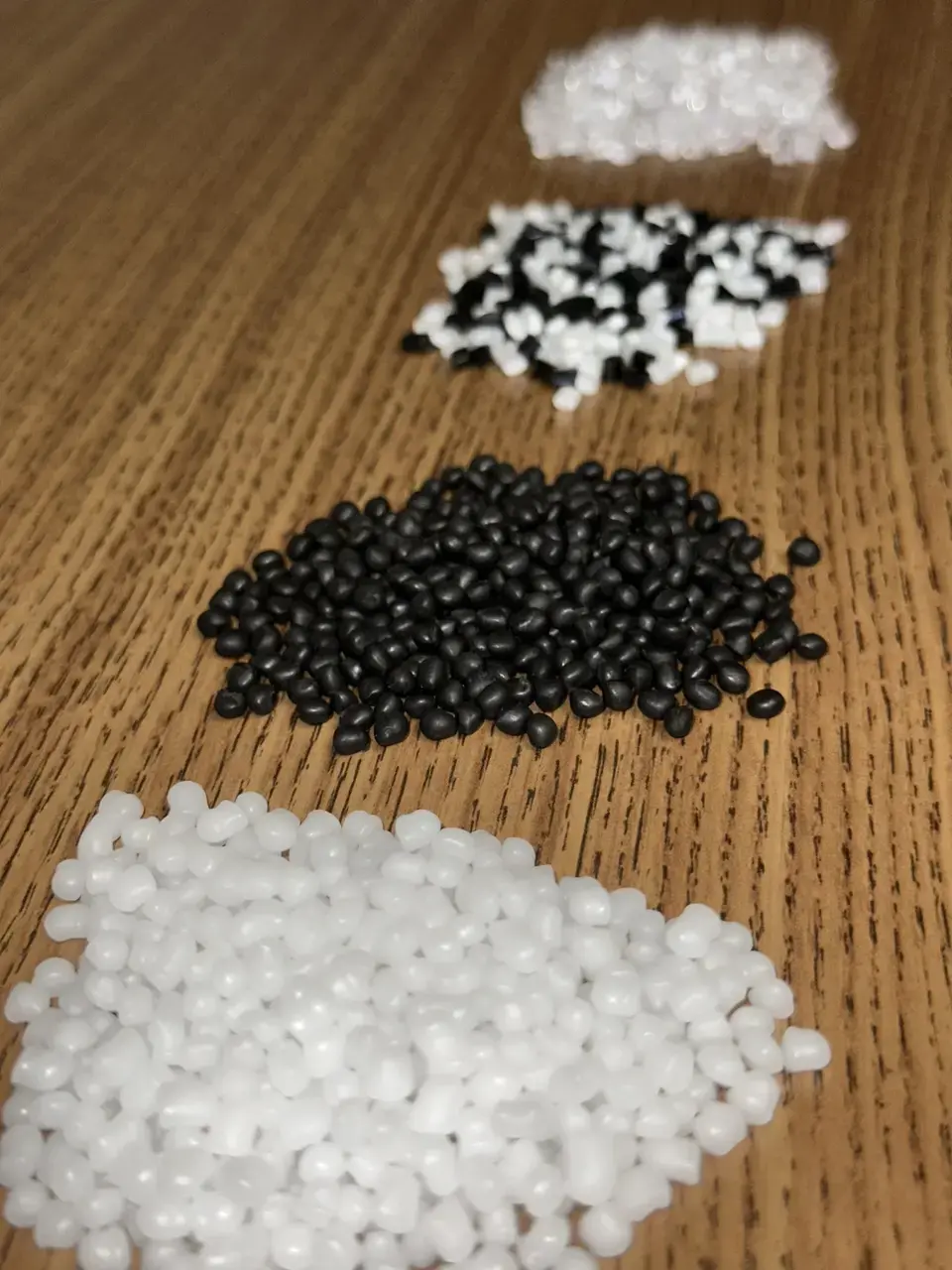
Understanding the Importance of Plastic in Your Project
Plastic play a pivotal role in numerous industries, from automotive and aerospace to consumer electronics and healthcare. Their lightweight nature, durability, and versatility make them a popular choice for a wide range of applications. Whether you're designing intricate components or structural elements, plastic offer unique advantages that can enhance the functionality and aesthetics of your project.
Moreover, plastic provides opportunities for complex geometries and customized solutions that may not be feasible with other materials. By harnessing the flexibility of plastics, engineers and designers can bring innovative concepts to life, pushing the boundaries of what is achievable in modern manufacturing processes.
In addition to their design versatility, plastic often contribute to cost savings and production efficiency. Compared to traditional materials like metal or glass, plastics offer a cost-effective solution without compromising on performance or quality. This balance of affordability and functionality makes plastic a compelling choice for projects across various industries.
Types of Plastic Materials Suitable for Various Project Needs
The world of plastic materials is vast and diverse, with each type offering unique properties and characteristics suited to specific project requirements. From the rigidity of polycarbonate to the flexibility of polypropylene, understanding the strengths and limitations of different plastics is essential for selecting the optimal material for your project.
Polyethylene, known for its chemical resistance and impact strength, is commonly used in packaging and construction applications, while ABS (Acrylonitrile Butadiene Styrene) combines toughness with dimensional stability, making it ideal for automotive components and consumer goods. By delving into the properties of various plastics, you can tailor your material selection to align with your project's performance demands.
Furthermore, considerations such as temperature resistance, UV stability, and recyclability play a significant role in material selection. Whether your project requires heat-resistant polymers for specialized applications or environmentally sustainable options for eco-conscious initiatives, the world of plastic materials offers a spectrum of choices to meet your diverse project needs.
When evaluating plastic materials, it's essential to factor in mechanical properties, chemical compatibility, and processing requirements. By conducting thorough research and engaging with material experts, you can make informed decisions that optimize the performance and longevity of your project's plastic components.
Factors to Consider When Selecting Plastic
Choosing the right plastic involves a nuanced evaluation of several key factors that influence the design, production, and functionality of your project. Material selection, design complexity, production volume, and end-use requirements all play a crucial role in determining the most suitable plastic components for your application.
Additionally, factors such as chemical resistance, impact strength, and surface finish can impact the performance and longevity of your plastic. Balancing these considerations with cost constraints and timeline requirements is essential to ensure the successful integration of plastic components into your project.
Collaboration between designers, engineers, and manufacturers is vital to navigating the complexities of plastic part selection. By leveraging expertise from across disciplines, you can address technical challenges, optimize material choices, and fine-tune the design of your plastic components for maximum efficiency and reliability.
Comparing Injection Molding vs. 3D Printing for Plastic Components
Injection molding and 3D printing are two widely used manufacturing processes for producing plastic components, each offering unique benefits and considerations. Injection molding, known for its high-volume production capabilities and cost efficiency, is ideal for manufacturing large quantities of standardized with high precision and repeatability.
On the other hand, 3D printing excels in rapid prototyping and low-volume production, allowing for intricate geometries and design iterations with minimal tooling costs. While injection molding is preferred for mass production of identical, 3D printing enables on-demand manufacturing of customized components, making it versatile for small-batch productions and complex geometries.
Factors such as production volume, design complexity, lead time, and cost considerations influence the choice between injection molding and 3D printing for plastic components. By understanding the strengths and limitations of each process, you can select the most suitable manufacturing method that aligns with your project's requirements and production goals.
Optimizing Cost-Effectiveness in Plastic Part Sourcing
Cost optimization is a critical aspect of sourcing plastic for your project, as it directly impacts the overall budget and profitability of your endeavor. By exploring different sourcing options, such as domestic manufacturers, overseas suppliers, or on-demand production services, you can mitigate costs while maintaining quality standards and production efficiency.
Vendor relationships, material procurement strategies, and production timelines all influence the cost-effectiveness of plastic part sourcing. Working closely with trusted suppliers, negotiating favorable terms, and streamlining logistics can contribute to cost savings without compromising on the quality or performance of your project's plastic components.
Moreover, adopting sustainable sourcing practices and optimizing material usage can enhance the eco-friendliness of your project while reducing long-term costs associated with waste management and environmental impact. By prioritizing cost-effectiveness in plastic part sourcing, you can achieve a balance between financial efficiency and project sustainability.
Embracing Plastic Innovation
As you navigate the realm of plastic for your projects, remember that each decision contributes to the overall success and efficiency of your endeavor. By carefully considering factors such as material compatibility, manufacturing methods, and budget constraints, you can streamline your project development process and achieve remarkable results. Embrace the versatility and innovation that plastic offer, and let them propel your projects to new heights.
Comentários