Understanding Injection Molding: A Beginner's Guide
- siliconeplastics
- Mar 7
- 5 min read
Injection molding is a fascinating and widely-used manufacturing process that can seem complex at first glance. This guide aims to break down the basic concepts of injection molding for those who are new to the field, providing clarity on its functions, benefits, and applications. Whether you're looking to start a career in manufacturing, design your own products, or simply understand this method better, this beginner's guide will cover all the essential information you need.
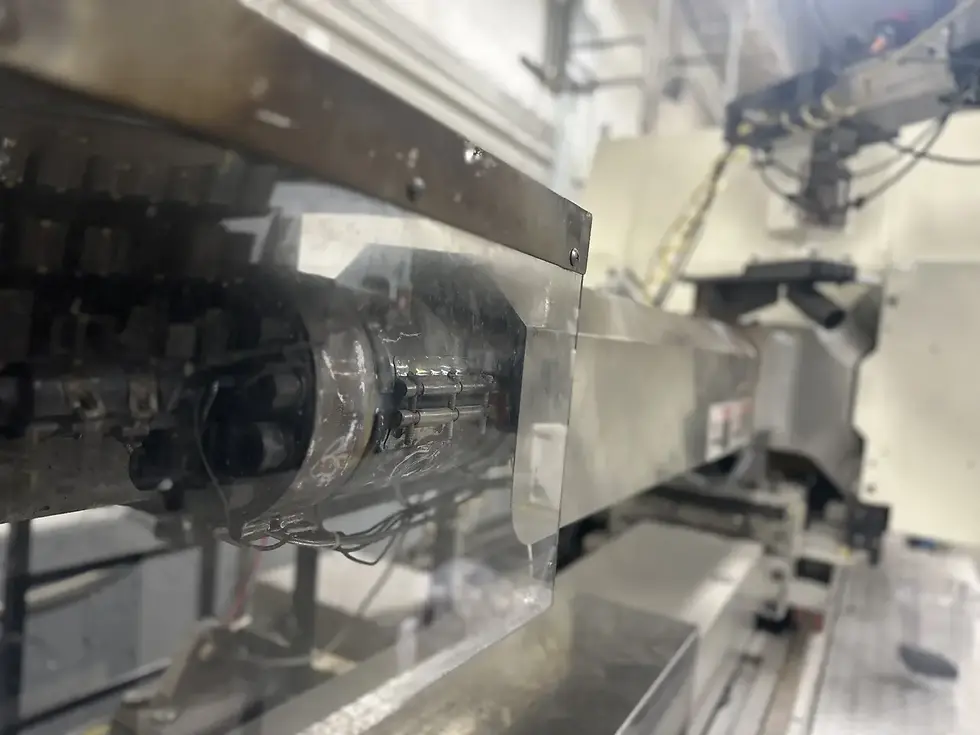
What is Injection Molding?
Injection molding is a manufacturing process that involves injecting molten material into a mold to create a specific shape. It is used predominantly for thermoplastics and thermosetting polymers, making it an essential technique in sectors ranging from automotive to consumer goods.
At its core, injection molding transforms raw materials into finished parts with incredible efficiency and precision. The process begins with heating the chosen thermoplastic or thermosetting polymer until it reaches a molten state. This material is then forced into a precisely designed mold, where it cools and solidifies into the desired shape. This method stands out due to its ability to maintain consistent quality and replicate intricate designs across thousands of units.
For beginners, grasping the fundamentals of injection molding is crucial. It serves as the backbone for many modern manufacturing processes. As you delve deeper, you'll discover various sub-processes and methodologies within injection molding, each tailored to specific industry requirements and product types.
The Injection Molding Process Explained
The injection molding process consists of several key steps: material preparation, injection, cooling, and ejection. Each phase plays a critical role in the quality and accuracy of the final product, and understanding these stages can help in troubleshooting issues that may arise.
First and foremost is material preparation. The chosen material must be dried and heated to achieve the right viscosity for injection. If moisture remains in the material, it can lead to defects in the final product, making this step crucial. Following this, the injection phase begins, where the heated, molten polymer is injected into the mold at high pressure. This phase requires precision machinery capable of exerting significant force to ensure complete filling of the mold.
Cooling is the next vital step. Once the molten material fills the mold, it must cool sufficiently to solidify into the desired shape. This cooling process can take anywhere from a few seconds to several minutes, depending on the complexity of the shape and the material used. Finally, the ejection phase occurs, where the mold opens, and the finished component is removed. This entire cycle repeats rapidly, allowing for large-scale production without sacrificing quality.
Materials Used in Injection Molding
A variety of materials can be used in injection molding, including plastics, metals, and even ceramics. The choice of material significantly impacts the functionality, cost, and overall performance of the finished product, which is vital for product designers to consider.
Plastics dominate the injection molding landscape due to their lightweight nature and versatility. Common examples include polyethylene, polystyrene, and polyvinyl chloride (PVC). These materials can be formulated to obtain a range of characteristics, from flexibility to rigidity. Another important category is thermosetting plastics, which, once set, cannot be remolded. This characteristic makes them suitable for high-heat applications.
Additionally, metals like aluminum can also be shaped through injection molding, although this process typically employs different machinery and techniques due to the higher melting points involved. Ceramics are increasingly being explored for specific types of components in specialized applications. Understanding the nuances of different materials will greatly enhance your ability to choose the right one for your specific application.
Advantages of Injection Molding
Injection molding offers several advantages, such as high production rates, consistency in product quality, and the ability to create complex shapes. These benefits make it a preferred choice for many manufacturers seeking to produce large volumes efficiently.
The high production rate of injection molding is one of its strongest selling points. Once the initial setup is complete, thousands of parts can be created in a matter of hours. This efficiency is particularly advantageous for industries requiring mass production, such as automotive and electronics. Furthermore, the consistency achieved through automated processes means that each product meets the quality standards expected by consumers, fostering brand loyalty.
Moreover, the ability to manufacture complex geometries with precision is revolutionary. Features such as intricate patterns, deep ribs, and geometric designs can be crafted seamlessly. This level of flexibility allows designers to innovate and bring groundbreaking products to market, ultimately benefiting consumers.
Common Applications of Injection Molding
This manufacturing method is widely used in various industries, with applications including automotive parts, household items, and electronics. Understanding where injection molding is applied can help you appreciate its significance in daily life.
In the automotive industry, for example, injection molding produces everything from dashboard components to exterior body panels. Lightweight, durable parts improve fuel efficiency while meeting stringent safety standards. In consumer products, items like containers, toys, and appliances benefit from both the aesthetic and functional advantages that this manufacturing method brings. Moreover, the electronics sector relies on injection molding for components that house delicate circuitry, showcasing its versatility.
As you explore these applications, you'll notice that virtually every industry has been touched by injection molding in some capacity. This offers a strong argument for understanding this process, as it often forms the backbone of modern manufacturing.
Challenges and Considerations in Injection Molding
While injection molding is highly advantageous, it does come with challenges, such as the initial cost of creating molds and the need for precise engineering. By being aware of these challenges, newcomers can better prepare for the complexities of the process.
The upfront costs associated with designing and manufacturing molds can be prohibitive for small businesses or startups. Depending on the complexity and size, molds can cost thousands of dollars, and if the design needs changes, it can exacerbate costs further. However, these initial investments can often be recouped through efficient production in the long run.
Moreover, precision is paramount throughout the entire process. Variations in temperature, pressure, or timing can lead to defects that jeopardize the integrity of the finished product. Thus, thorough testing and validation are crucial steps that cannot be overlooked. Understanding these challenges facilitates informed decision-making and strategic planning.
Getting Started with Injection Molding
For those interested in diving deeper into injection molding, it is crucial to educate yourself on design principles, machine operation, and material selection. Numerous resources, including courses and workshops, can enhance your understanding and skills in this field.
Begin by familiarizing yourself with fundamental design principles such as draft angles, wall thickness, and undercuts. These elements are critical for creating molds that not only function effectively but also maximize efficiency. Next, consider exploring machine operation; understanding how these machines work allows you to troubleshoot potential issues and optimize performance.
Additionally, material selection plays a vital role in the injection molding process. Research various materials, their properties, and how they interact with the mold and process parameters. Online forums, academics, and local workshops offer a plethora of insights and mentorship opportunities that can guide you on your journey. With the right education and practice, you can harness the potential of injection molding to create innovative designs.
Wrapping Up: Embracing the World of Injection Molding
In summary, injection molding is a key manufacturing process that offers efficiency, versatility, and innovation opportunities. By understanding its fundamentals, you can not only appreciate the products it creates but also make informed decisions if you choose to venture further into this industry. Embrace the possibilities that injection molding presents and take your next steps, whether that's designing a product or pursuing a deeper knowledge of manufacturing technologies.
Comentarios